In this interview with WishGarden Herbs' Quality Control Manager, Nicole Anderson, we go beyond the ingredient list to find out exactly what goes into every bottle of WishGarden's herbal formulas when it comes to ensuring a safe, high-quality product!
Q. What is your role at WishGarden?
I'm the Quality Manager, which means I run both Quality Assurance and Quality Control. Day to day, I make sure that my team has everything they need to ensure that what's coming into the facility and what's going into the bottles is high quality and is what it says it is. I also write SOPs (standard operating procedures) and oversee cleaning, processing, and other operations as needed. I'm basically there to make sure that whatever we have going out the door is going to be safe for our customers.
I didn't have a background in herbalism when I started at WishGarden, but I graduated from the University of Colorado with a degree in evolutionary and ecological biology, which has been helpful in this role. I've been here for eight years, and I actually started off on the packaging line and worked my way up from there to Quality Manager!
Q. What's the difference between quality assurance and quality control?
Quality assurance is more about documentation and making sure that we are following all of the regulations set by the U.S. Food and Drug Administration (FDA). That also involves making sure everyone we hire is trained properly. Quality control is more hands-on in the lab where we're actually testing all of our ingredients and products. We're responsible for identifying the herbs as they come in and testing the formulas and packaging every step of the way.
Q. A lot of WishGarden's herbs come from small and local farms. Are there any quality control challenges that come with that versus more commercial providers?
We love to buy from local vendors or smaller global vendors, but they don't always have the experience or the ability to send their material out for testing before it gets to us. So in addition to our in-house testing we also send a lot of our raw materials out for third-party laboratory testing to check for any microbial issues. We also work with them on education around good manufacturing practices (GMPs) and adhering to FDA regulations.
Aminta, WishGarden's Body Care Specialist, with a shipment of fresh, local Arnica.
Q. Now for the big question: How does the quality control process work from start to finish?
When we receive a batch of herbs, we first weigh it to make sure it's the correct amount that we ordered from the supplier. That can really vary! For example, we might receive 3,000 pounds of Yerba Santa at one time, because we use it in so many of our formulas (including Kick-Ass Immune Activator, which is our biggest selling product). Other times we might receive two pounds of a rarer herb that we use sparingly in just one or two products.
Next, we confirm that the shipment contains the correct herbs. Of course we know what they're supposed to be based on the certificate of analysis (when one is available), but we still make sure they've been labeled correctly and that there aren't any other herbs or materials mixed in. We have identification specifications for all of the herbs we use, which is stored in the same software we use for our inventory control, so when we receive something, it gets entered into this program, which then gives us all the specifications for that particular plant.
If we can't identify a batch of herbs or are concerned that they may be adulterated in some way, we will send them to a third-party lab for identification confirmation. We also send most of our herbs for third-party microbial testing.
Once we're sure we have the correct herbs and that there are no microbial issues, we do our own quality-control testing in our lab, which is right next to both Production and Packaging. One of the most exciting things we do in-house is organoleptic testing, which is a fancy way of saying that we test our products using our senses — sight, smell, feel, and — of course — taste!
Hard at work in the WishGarden Herbs Quality Control lab.
We test everything from the raw herbs to the single extracts to the blends to the finished product that goes into the bottles, so everything is tested several times before it makes it out the door and to the consumer. We also assess all the packaging, including the bottles and droppers and pump tops, and we design the labels (including the beautiful artwork!) and make sure they match what's actually in the bottles.
Q. Sounds pretty rigorous!
Absolutely. We've got an in-depth understanding of what expectations and specifications we need to meet to ensure that what is going out in each bottle meets our standards and those of the FDA.
Q. Finally, what's your favorite thing about working at WishGarden?
I'd say the community that we've formed. I love my team, and the entire WishGarden family. I've been able to form life-long friendships with some of the people I've met here. They've taught me so much about the herbal world and community.
What to learn more about WishGarden Herbs' products or processes? Check out our Frequently Asked Questions.
Interviewer Valerie Gleaton is a professional writer and editor. She has a master's degree in journalism from the University of Colorado at Boulder, where she also earned a certificate in science and environmental reporting.
For educational purposes only. This information has not been evaluated by the Food and Drug Administration. This information is not intended to diagnose, treat, cure, or prevent any disease, or sell any product.
Recommended Products
Further Reading
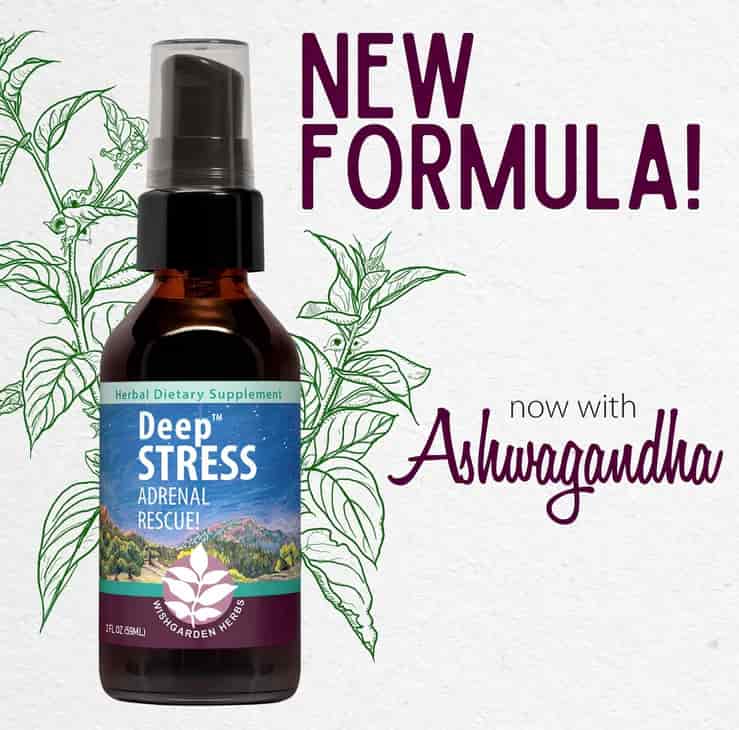
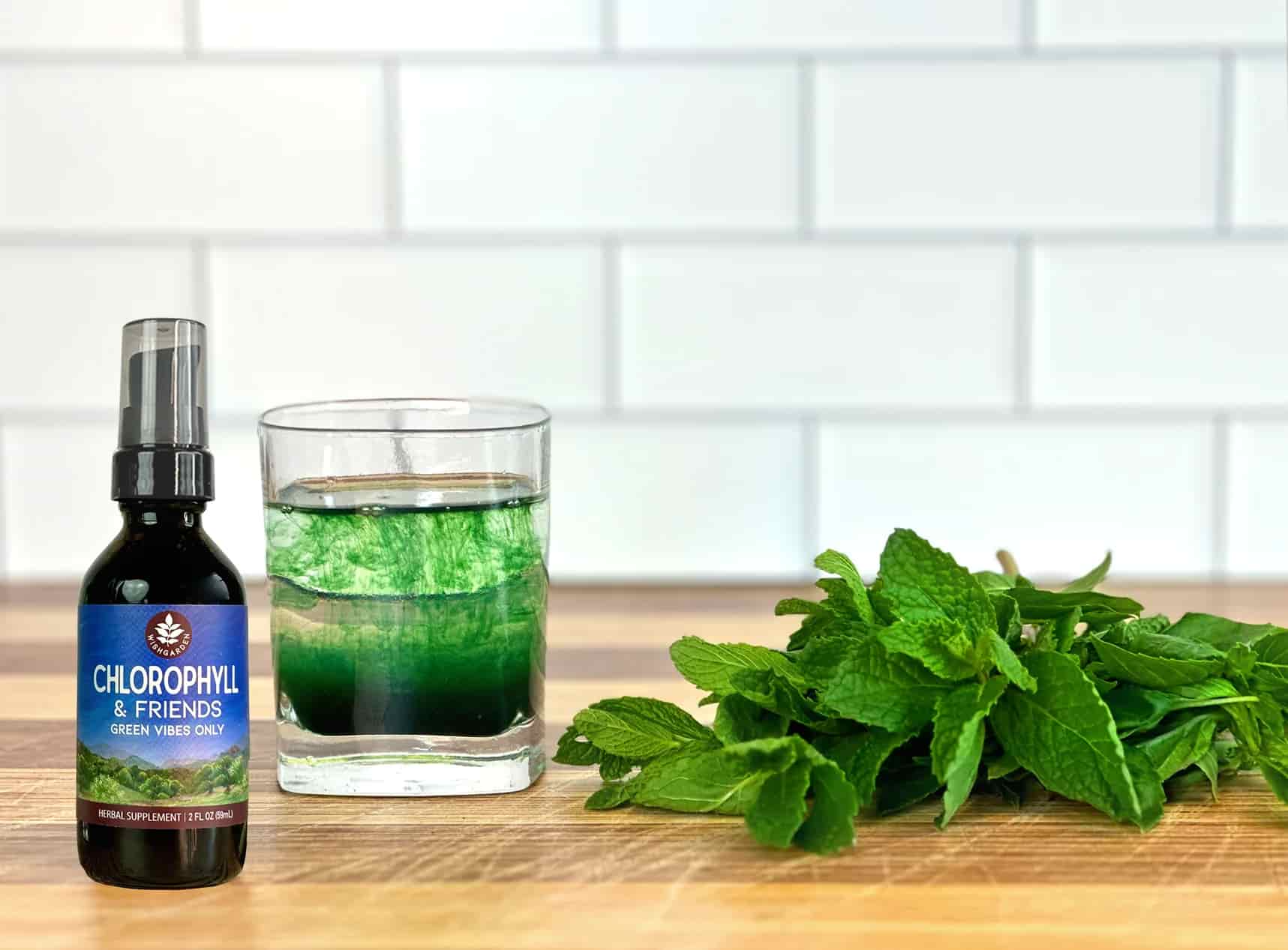
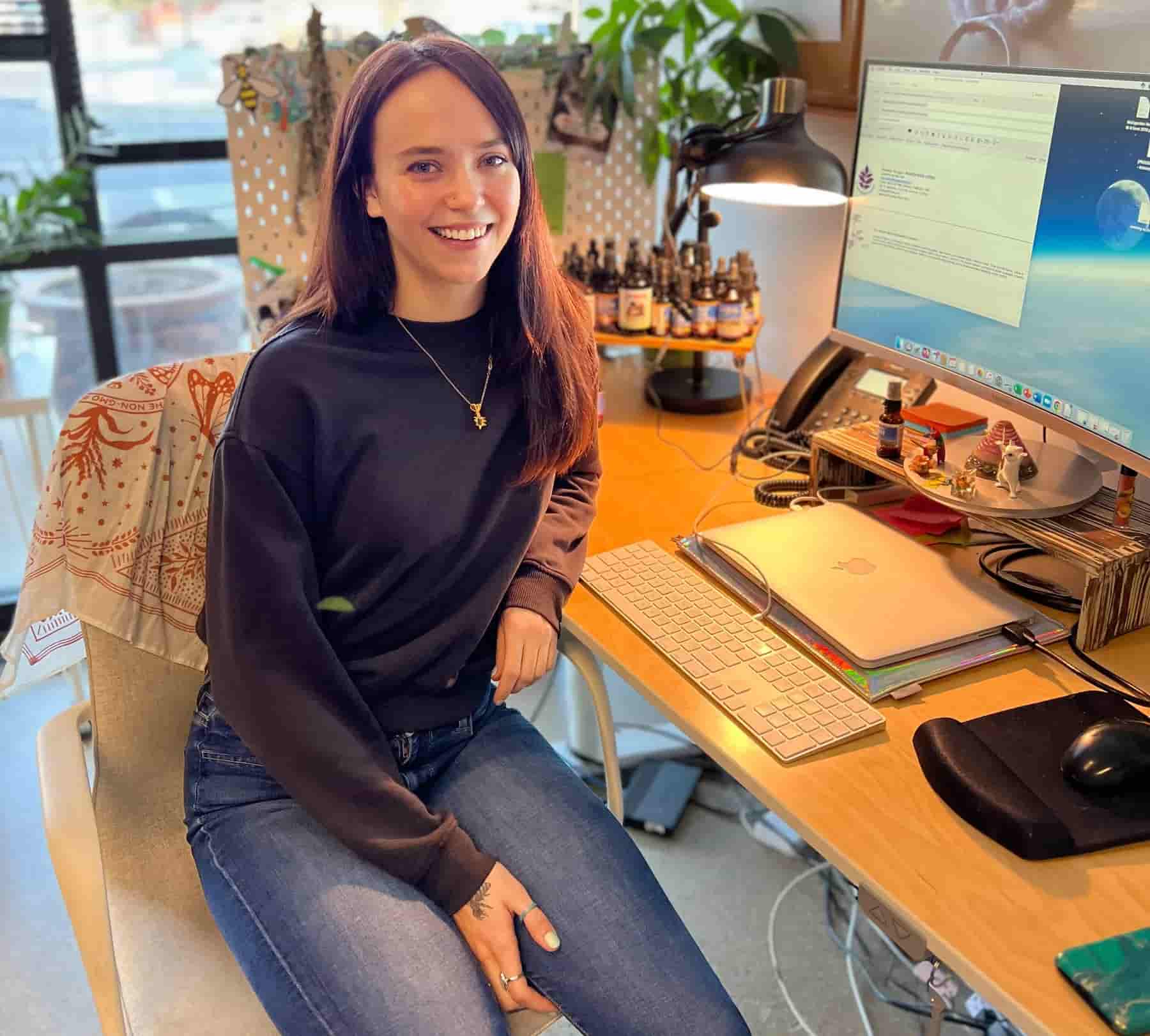
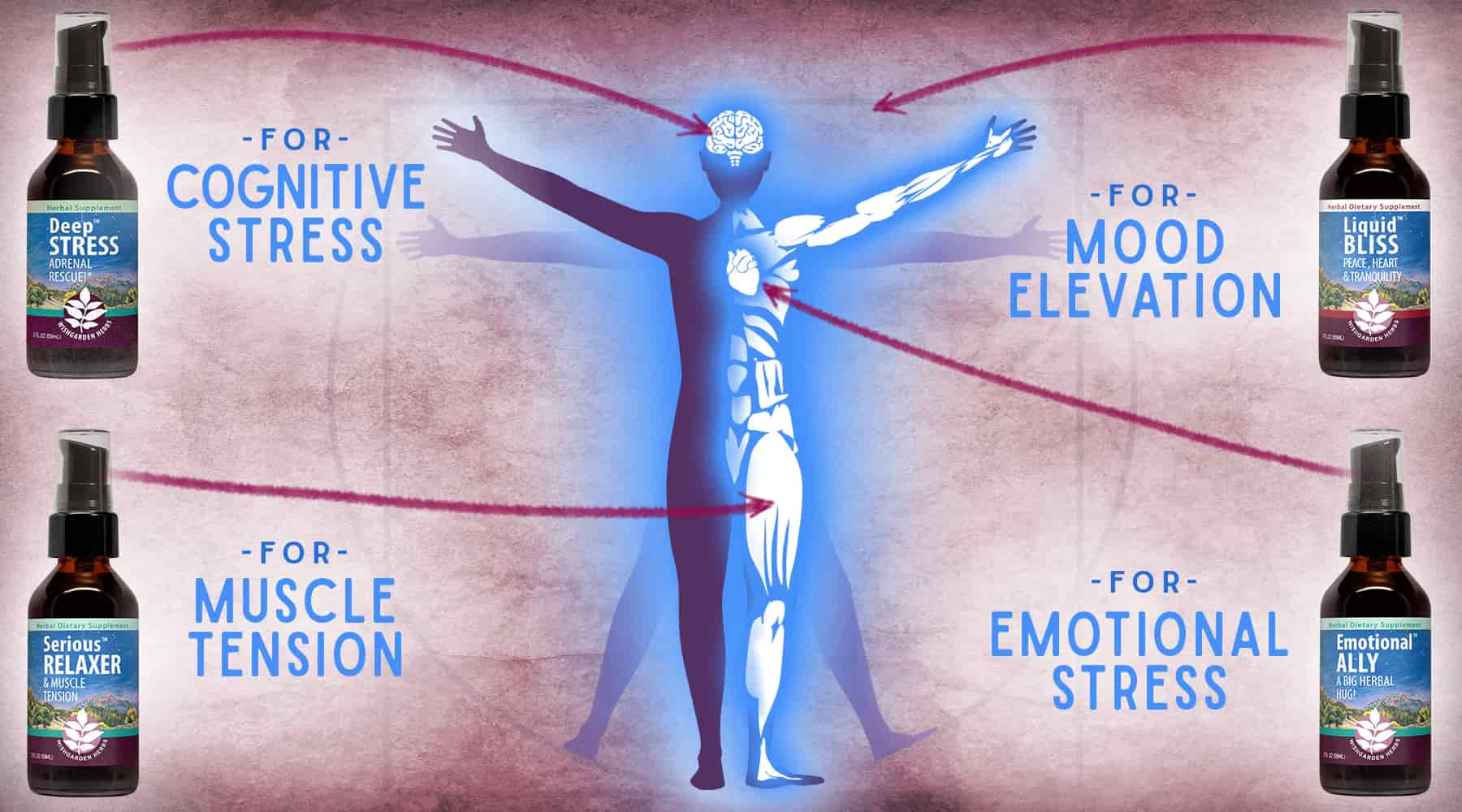
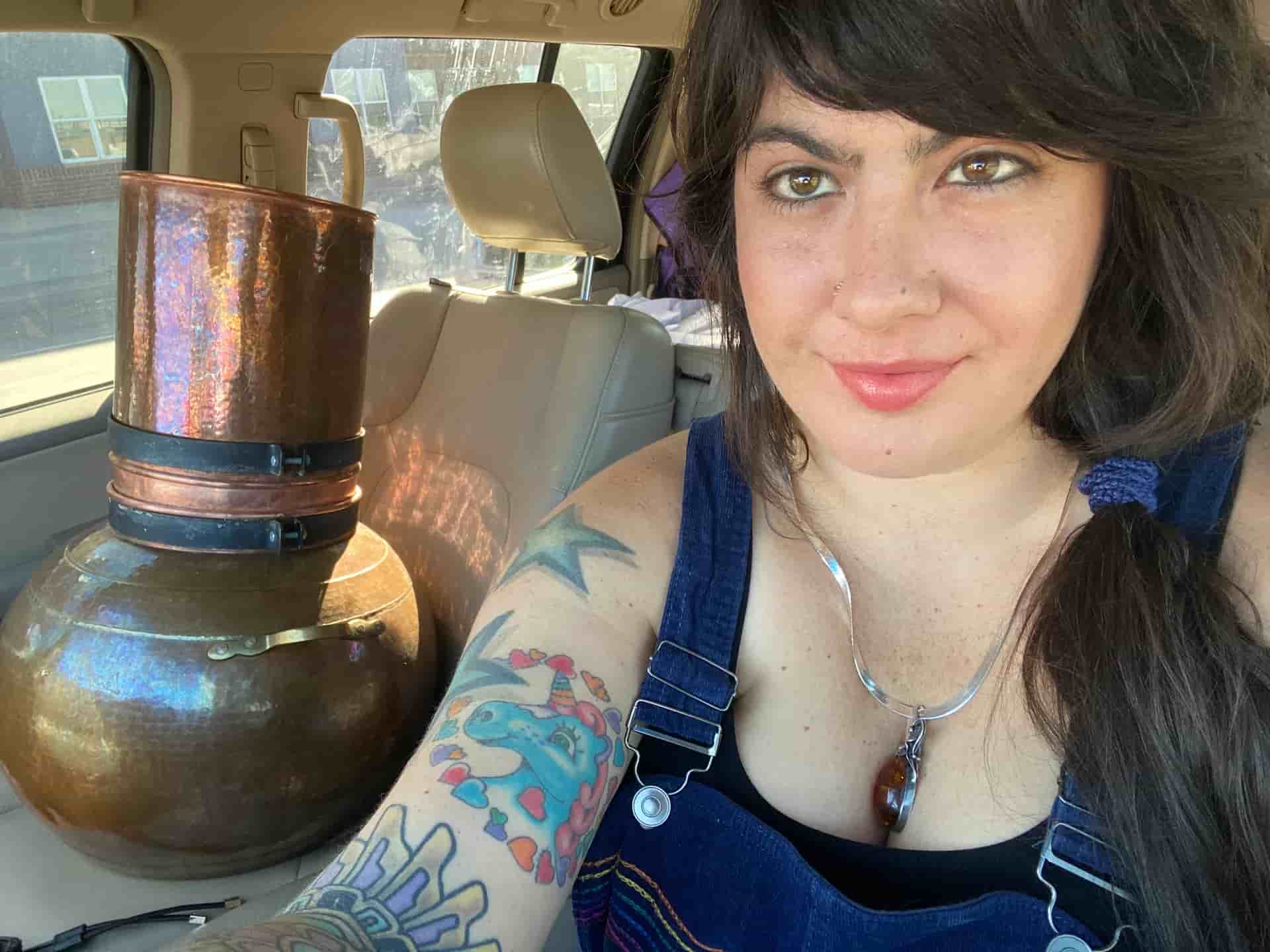